Everything You Need to Know About Electric Forklift Batteries
October 27, 2021
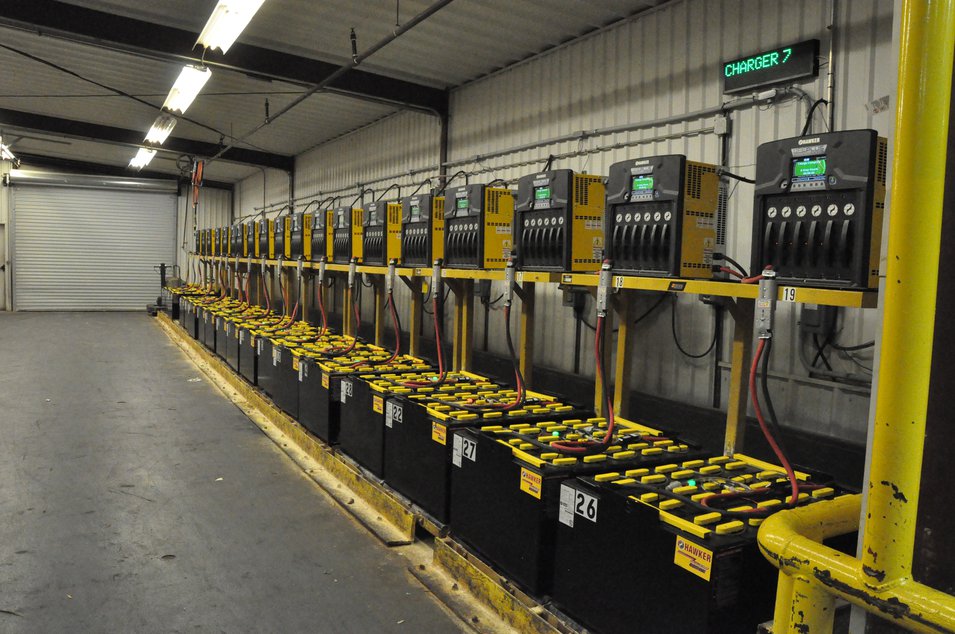
Select the Right Size & Type of Battery for your Forklift
Selecting the proper battery technology for your electric forklift is a critical decision. Whether you are upgrading an existing battery, or purchasing a new forklift, you need to thoroughly assess battery options as it can have a direct impact on the forklift performance, business productivity, and bottom line.
There are predominantly two types of battery technologies powering commercial forklifts - Lead-acid and Lithium-ion. In this guide we will compare them on different parameters like- technology, costs, maintenance, and charging needs, to help you reach an informed decision. Before getting into a detailed comparison, let’s briefly look at the working of these two technologies and tips on battery sizing.
1. Technology
Lead-acid Batteries
A lead acid battery consists of lead plates as electrodes, immersed in an electrolytic solution of sulfuric acid and water. Electricity is generated by a chemical reaction between lead and sulphuric acid. Water gets lost during the chemical reaction so regular refilling of water in the battery is necessary to maintain the required level.
Lithium-ion Batteries
There are multiple types of lithium ion batteries are available in the market depending on the type of cathode material used in them. Some of the lithium-ion battery options include lithium cobalt oxide, lithium manganese oxide and, lithium iron phosphate (LFP), of which LFP is one of the most popular chemistries in the modern material handling industry. LFP offers higher safety, and current and has a lower environmental impact as compared to some other types of lithium-ion batteries.
2. Forklift Battery Sizing
Selecting the right battery size is critical to ensure that your forklift can perform at its peak and lift the load it is rated to lift. There are three parts of battery sizing that you need to look at-
1.Battery Voltage & Ampere Hour
Forklift batteries are typically available in four voltage options and selecting the right one is the most important part of battery sizing. An oversized battery may cause severe, and irreversible damage to the truck so be sure to know what kind of voltages your truck can handle. Generally, the voltage is marked on the spec plate of most forklifts.
It is advised to choose a battery with the highest ampere-hour for the approved voltage rating to get maximum power for your forklift.
While the table below gives you an overview about which battery voltage is suited for which equipment type, be sure to speak with your local battery specialist to understand what battery size is appropriate for your forklift.
Voltages | Type of Forklift |
---|---|
24-Volt / 36-Volt batteries |
Rider Forklifts Stackers Pallet Jacks Order Pickers Narrow Aisle Forklift |
48-Volt / 80 Volt Batteries |
Reach Trucks Counterbalanced Electric Forklifts |
120 Volt Batteries and above |
Yard Vehicles Shunt Trucks |
2.Battery Dimensions
Next, you need to measure the forklift’s battery compartment size and make sure that the battery fits in well. The battery needs to fit the compartment properly. A battery that is too big, or too small could pose a safety hazard.
3.Battery Weight
Check the spec sheet or spec plate to find out the Minimum and Maximum battery weight requirements for the truck. If you pick a battery which is heavier than the maximum weight then you run a risk of putting unnecessary strain on various equipment parts, even voiding the manufacturer's warranty. In many cases, battery also acts as a counterbalance for your truck. A battery lighter than the minimum required weight may reduce your trucks lifting capacity and cause safety issues. When changing the battery on any forklift, a new spec plate may be required to outline the altered capacity of the machine based on any weight change. The battery of an electric forklift acts as a counterweight to the machine and is critical to its lift capacity.
In the next part, we will look at a detailed comparison of the lead-acid and lithium-ion technologies on various vital parameters.
3. Lead-acid vs Lithium-ion Battery Comparison
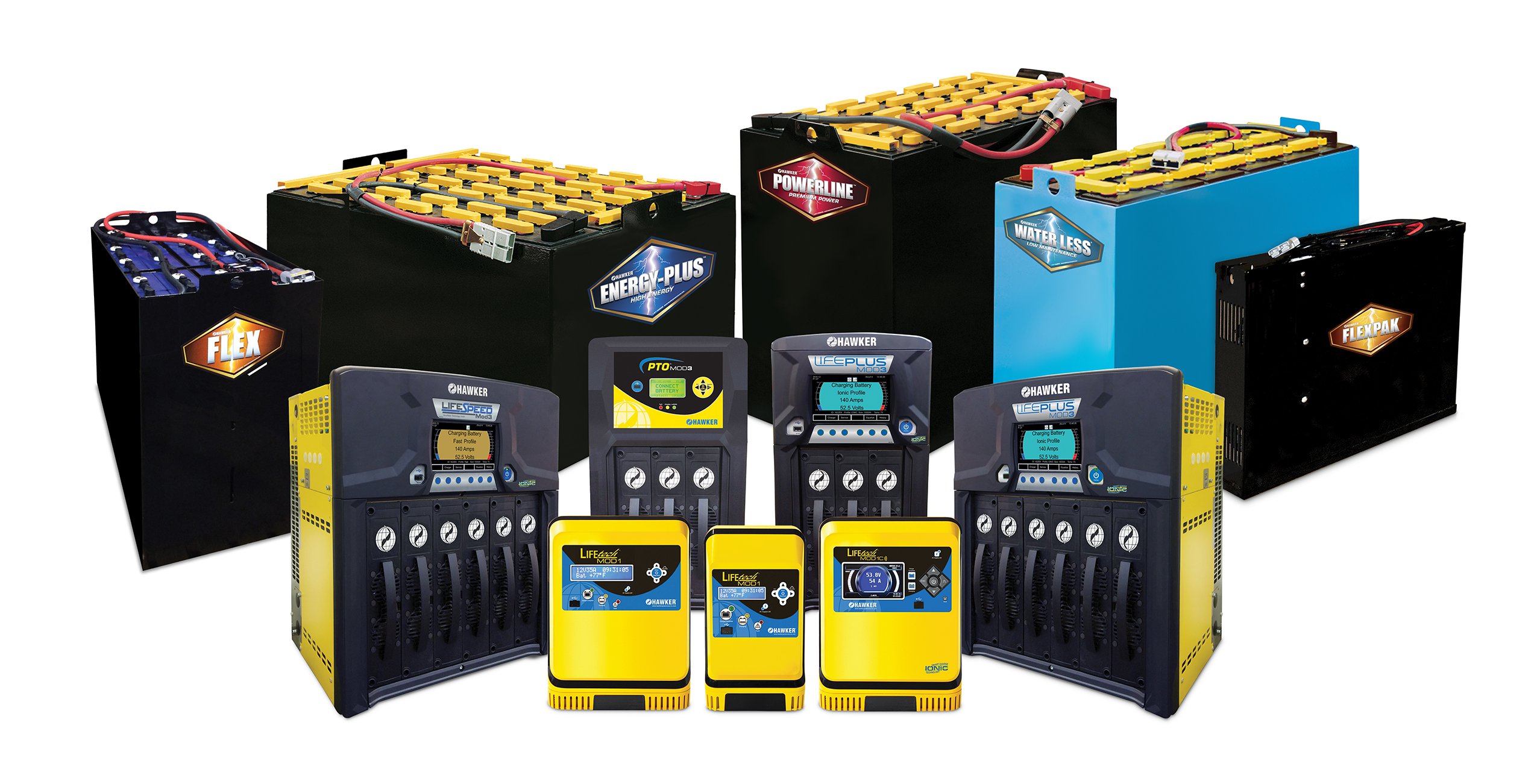
3.1 Single-Shift vs Multi-Shift Operation
Lead-acid batteries:
If you operate your business for 16 or 24 hours a day, battery charging times become crucial to ensure smooth running of your operations since a typical battery discharges in about 6-8 hours. A lead acid battery needs about 8 hours to charge followed by 8 hours of cooling period, making it a total of 16 hours before it can be used again. So, for a multi-shift operation, you may need 2-3 lead-acid batteries per forklift. If you do not carry multiple batteries for each forklift, you may experience downtimes due to unavailability of equipment, directly impacting the bottom line.
Lithium-ion batteries
A lithium-ion battery gets fully charged in less than 2 hours and does not require a cooling off period like lead-acid batteries. Li-ion batteries can also be charged in 15-30 minutes spurts, often known as opportunity charging, making it possible to charge them during lunch breaks or anytime the forklift is idle for a few minutes. You to carry out multi-shift operations with just one battery per forklift, thanks to increased fleet availability because of fast charging.
Bottom line
While there is a huge difference in the charging times, both types of batteries usually last the same number of hours (between 6-8) after the full charge. If you have a single-shift operation and a small fleet size, you can make it work with lead acid-batteries. As your fleet size and operations grow, lithium-ion batteries become unavoidable to carry-on uninterrupted operations.
Speak with one of our specialists to get battery recommendations based on your operations.
3.2 Infrastructure and Resources Available for Charging
Lead-acid batteries
Since you may need to carry multiple lead-acid batteries per forklift, you also need to account for additional storage space for them. Additionally, you must ensure a safe storage environment- one which is away from hot air ducts and other heat sources, does not get direct sunlight, and is maintained at room temperature or lower.
You also need to follow a safe charging process for lead-acid batteries and allocate resources for the same. For every charge, the battery must be removed from the forklift and placed on the designated charging rack, making it a labor intensive process. Because the battery is heavy, it may require trained personnel to use a lifting equipment for moving it from forklift to charging rack and vice-a-versa.
That said, most of the facilities today are equipped with electrical supply infrastructure suitable for the lead acid batteries. You may not need to make any significant investments towards the battery charges, outlets, and cabling.
Lithium-ion batteries
You don’t need the additional storage infrastructure while opting for lithium-ion batteries as you don’t need multiple batteries per forklift. Even while charging, you can let the battery sit inside the forklift itself, making the process simple and cost-effective. You can simply connect the battery to a charger by driving your forklift to a power outlet.
Since Li-ion battery charging is much faster, they also need higher input current for the same. You may need to conduct an energy audit of your facility to understand if you need to revamp your electrical infrastructure for efficient charging of Li-ion batteries. It will be a one time cost of adopting the Li-ion batteries for powering your forklifts.
Bottom line
Lithium ion batteries can help you save valuable space, and time of your people owing to its faster and simpler charging process. If you plan to purchase lead-acid batteries, you should account for these additional, and often hidden, infrastructure costs.
On the other hand, you may need to upgrade your electrical infrastructure for adopting Li-ion batteries as their chargers usually need higher input current.
3.3 Maintenance
Lead-acid batteries
If not maintained properly, lead-acid batteries undergo a chemical process called battery sulfation, which can cause them to break down. To avoid this, it is important to maintain the lever of water in the electrolyte. Topping up the battery with distilled water at regular intervals is essential to maintaining the health of a lead-acid battery.
Watering the batteries for a large fleet can be a tedious and costly process. You need to allocate trained personnel to undertake this procedure and ensure that they follow the safety protocol while doing so.
Lithium-ion batteries
Lithium-ion batteries are much easier to maintain as they do not need to be topped with water and does not require any such frequent maintenance procedures.
Bottom line
Regular watering of lead-acid batteries is inevitable to maintain their output, something which you don’t need to do with lithium-ion batteries. Tedious and cost-intensive maintenance procedure is one of the major drawbacks of lead-acid batteries.
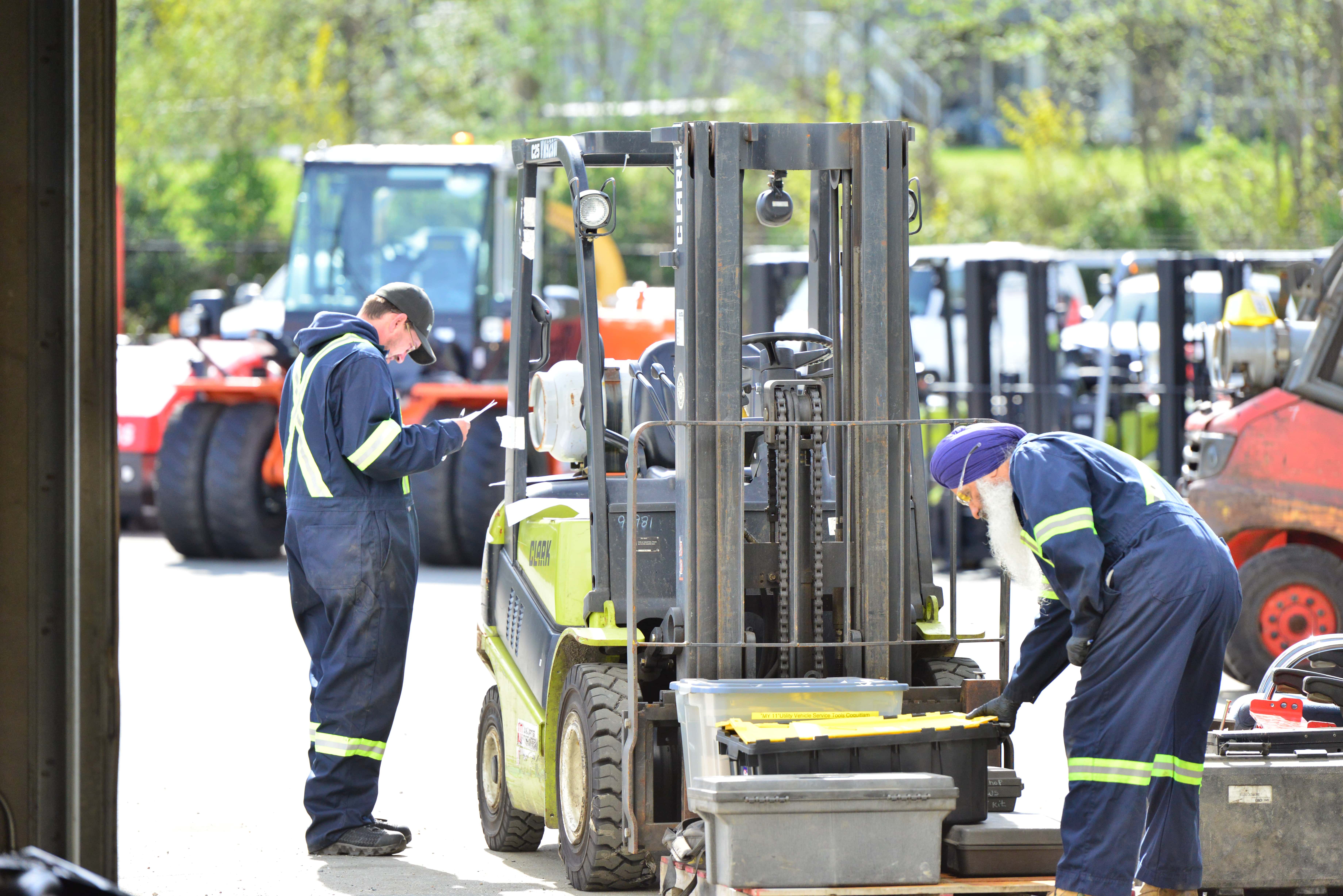
3.4 Safety
Lead-acid batteries
Since the lead-acid batteries are made up of two high-risk chemicals- sulphuric acid and lead, they could pose a safety hazard for you and your team. There is a risk of sulphuric acid contacting skin, and eyes of those performing the maintenance procedure so you need to ensure wearing of personal protective equipment (PPE) like splash-proof goggles, acid resistant apron, face-shield, and rubber gloves.
Lead-acid batteries may also produce an explosive mix of hydrogen (H2) and oxygen (O2) gases while being charged. If the charging room is not ventilated appropriately, there is a risk of explosion. Among other measures, you need to install hydrogen sensors at the ceiling of the rooms where lead-acid batteries are charged.
Over-charging vented lead-acid batteries, especially old ones, can produce a highly toxic fume called hydrogen sulfide (H2S). If such an event occurs, you may need to evacuate the area to ensure no one is exposed to this dangerous gas.
Lithium-ion batteries
Lithium-ion batteries are considered much safer as compared to lead-acid batteries since they do not pose as many health hazards for those working with them. These batteries are completely sealed and do not have to be opened for watering, reducing the danger of electrolyte spills, toxic fumes, or sulphation as in the case of lead-acid batteries.
Bottom line
Lithium-ion batteries can be considered much safer than the lead-acid batteries. Health and safety are paramount in any work environment, and you need to account for costs associated with training, labor, and infrastructure to create a safe environment when using lead-acid batteries.
3.5 Battery Lifespan
Lead-acid batteries
A well-maintained lead acid battery has a lifespan of 1000 to 1500 charging cycles. Important point to note here is that even if you charge a lead-acid battery for a short period, say 15 minutes, that counts as one charging cycle. This further reduces the lifespan of a lead-acid battery if you do not carefully charge it to 100% every time.
In addition to maintenance, the timing of charging can also affect a lead-acid battery’s lifespan. You should not leave a lead-acid battery in a state of partial discharge and need to immediately charge them to ensure their performance and longevity.
Lithium-ion batteries
A Li-ion battery lasts anywhere in between 2,000 to 3,000 charging cycles. Unlike lead-acid battery, lithium-ion is considered to have gone through one charging cycle only when it gets 100% charged. Intermittent charging of a few minutes adds to the convenience but does not reduce the lifespan of a li-ion battery.
Also, leaving a li-ion battery in a state of partial discharge does not negatively affect their lifespan as they don’t suffer any damage.
Bottom line
The overall lifespan of the batteries you chose determines how often you will need to replace them. Li-ion batteries can help you save on the recurring replacement cost considering they have almost double the cycle life as compared to lead-acid batteries.
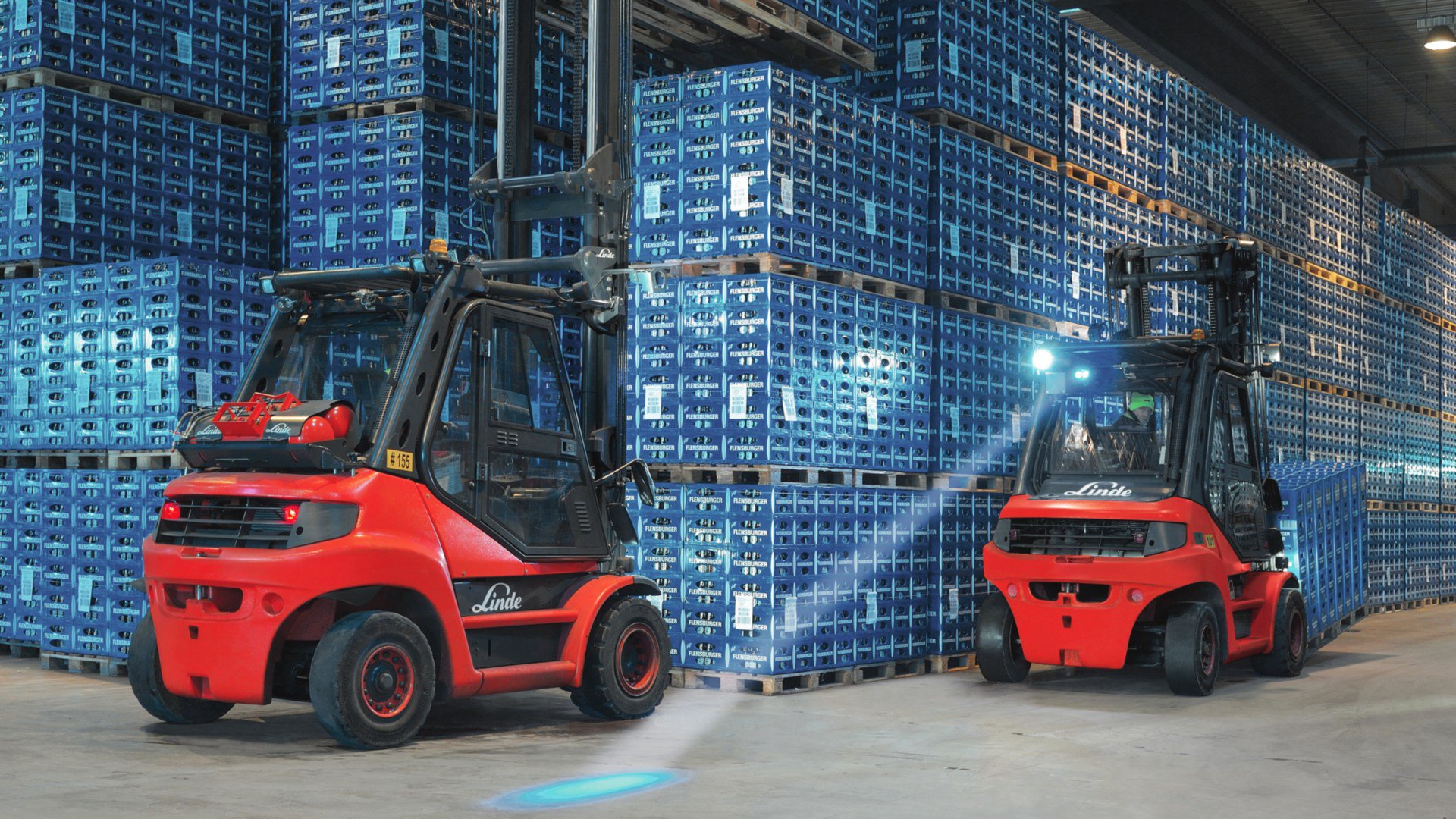
3.6 Energy Efficiency
Lead-acid Batteries
Lead-acid batteries bleed energy while charging, discharging and even while sitting idle. As a result, only about 80% of the energy used for charging the battery is actually available as the output, making lead-acid batteries energy inefficient and bringing up the electricity costs.
Lithium-ion batteries
Lithium-ion batteries can be considered much more energy efficient as the losses are minimal and most of the energy used for charging is available as output, as much as 99% in some cases.
Bottom line
Lithium-ion batteries can help you reduce electricity costs as they provide more output owing to minimal energy losses. You can expect savings up to 30% as compared to lead-acid batteries which are notorious for bleeding energy.
3.7 Upfront Cost
Lead-acid Batteries
The upfront cost of a lead acid battery is quite low as compared to other types of batteries.
Lithium-ion Batteries
Initial investment for a li-ion battery may be almost twice as much as that for a lead-acid battery.
Bottom line
Owing to the low upfront cost, lead-acid batteries may be a suitable option in certain business scenarios as mentioned in the point #1. Looking at the Total Cost of Ownership (TCO) is critical as it gives a holistic and long term picture when making such investments.
3.8 Total Cost of Ownership (TCO)
Let’s compare TCO for these two types of batteries for a typical two shift operation.
Parameter | Lead-acid batteries | Lithium-ion batteries |
---|---|---|
Initial cost | 2 batteries (One battery/shift) | 1 battery |
Maintenance cost |
Related to watering and, battery swapping per shift | Not required |
Electricity for charging |
Higher cost as they bleed energy and usable output is much lesser than the input |
Up to 30% savings due to higher energy efficiency - provides up to 95-99% of energy stored as output |
battery replacement Cost |
Every 1500 charging cycles 1 cycle= every time it is plugged in even if it is just for a 15 minute coffee break |
May extend up to 3,000 charging cycles 1 cycle= 100% charge |
Total Cost of ownership | $$$ | $$ |
Purchasing batteries for your fleet is a major investment decision, one which you should make considering various parameters that we have documented in this guide. Having compared the two popular battery technologies on the critical parameters, it is safe to conclude that even-though lead-acid battery technology is the oldest one, it may not be the best option for your material handling needs.
You can refer the following table for a quick comparison of the two most popular battery technologies.
4. Quick Comparison Table
Following table summarizes the comparison between lead-acid and lithium-ion batteries for your quick reference.
Parameter | Lead-acid batteries | Lithium-ion batteries |
---|---|---|
No. of shifts with one battery | 1 | Up-to 3 |
Charging time | 8 hours | 2-3 hours |
Opportunity charging | Possible, however battery life reduces drastically | Charging for as low as 5-10 minutes whenever possible |
Safety & Health Risks | High | Low |
Watering the battery | Yes | N/A |
Maintenance Cost | High | Low |
Battery LifeSpan | ~1500 cycles | 2000 - 3000 cycles |
Electrical Infrastructure | Use existing | May need Upgrade |
Replacement cost | High | Low |
Energy Efficiency | Low | High |
Electricity Cost | High | lower Save up to 30% because of higher energy efficiency |
Upfront Cost | Low | High |
Total Cost of Ownership | High | Low |
Environment Friendly | No | Yes |
Williams Machinery offers complete material handling solutions. Our specialists can help you select the right forklift and battery for your business needs.